Moreover, embrittlement owing to irradiation or temperature has to be mastered in order to keep away from rupture within the reactor or in the course of the again-finish of the cycle (handling, washing, and so forth.). Cold-labored austenitic steels (with composition closed to that of the cladding) have been used first but are actually regularly changed by more swelling-resistant ferritic–martensitic steels (9Cr type), in so far as the height wrapper temperature, decrease than that of cladding, allows avoidance of thermal creep problems.
Today, Zircaloy-2 and Zircaloy-four are extensively used. Phase transformation of Zirconia is, however, of great concern.
Cladding equipment is generally designed to swimsuit a selected product or a group of products; this particularly applies to the items required for uncoiling of the strip and the feeding tool. The materials and floor of the rolls as well as their geometrical shape (cylindrical or crowned) are very important.
In addition to metallurgical factors, water chemistry has a powerful influence on the corrosion course of in zirconium alloys. The control of water chemistry as required in numerous reactor techniques embody suitable additions of lithium hydroxide, boric acid, hydrogen/deuterium, oxygen, iron, and zinc. In PWRs, boric acid is added to the coolant water for reactivity management. The pH of the coolant is adjusted by addition of lithium hydroxide which renders the coolant barely alkaline, in order to cut back the corrosion rates of structural supplies (stainless steels and Inconels) in the primary warmth transport circuit and thereby inhibit deposition of corrosion products on the fuel cladding. Radiolysis of water produces oxidizing species which enhances oxidation rate of zirconium alloys in the radiation environment .
The Building Research Establishment (BRE) has been commissioned to undertake this project. This programme is on-going and tests are anticipated to conclude in the summer.
Zry production strategies now offer far better control of gaseous impurities than early fabrication know-how, so the original reason for including tin is moot. Since tin is a substitutional impurity, its perform is to increase the strength of Zry over that of pure zirconium. 1.5% tin, and the balance being iron, nickel, and chromium.
This is a major cladding failure that admits steam into the rod with the accompanying potential for a extra serious secondary failure because of hydriding. The combination of conditions (vulnerable metal, tensile stress, and chemical enhancer) that produces the first defect is termed pellet–cladding interplay (PCI). scale that grows around them during in-reactor operation. This loss of the insulating properties of the oxide is believed to speed up the corrosion rate.
laser. The clad substrates confirmed improved oxidation characteristics compared with the original alloy. Conventional methods for cladding have employed tungsten-inert fuel welding, plasma spraying, and flame spraying.
The low burnup habits is controlled by components corresponding to pellet densification and gasoline-clad hole closure, however at higher burnups conductivity degradation turns into increasingly important, driving the temperatures up to and past the level the place gaseous and risky fission products start to be launched from the gasoline. The consequences of this are considered further in later sections. due to their corrosion resistance to acids and bases and their low neutron-absorption charges. Zircaloys have anisotropic physical, mechanical, and chemical properties. Within the oxide layer, the alloying elements influence the atomic transport such that the alloying concentration determines the corrosive behavior, with high alloying concentrations (above ∼0.6%) providing safety towards oxide development.
In our cladding solutions we think about the styling and colors, alternative of materials, lighting design and general setting of the building as key CI elements, so that everything matches your particular person requirements. Although the thermal properties of façade coverings used to be of major importance, today corporate identity (CI) elements are essential to the design of the panels. ACM (aluminium composite), glass, pure stone and sheet metal are just some of the materials that can be utilized in the wide range of plate-holders and sections. , where T is absolutely the temperature and β is the burnup.
The impact of thermal conductivity degradation on the performance of the gas is illustrated in Fig. 1 . This reveals the results of calculations in which the facility in a rod is artificially held at a relentless degree.
The process is often used to create a protecting coating for increased functionality, as well as restore damaged or worn surfaces. Laser cladding permits extended life of kit and machinery in which elements are uncovered to corrosion, wear or impact. For instance, the development gear industry applies this expertise to their merchandise to increase wear resistance and maintain tools in service longer. A excessive-power laser is used as the heat source in laser cladding. During the process, a floor layer is created by means of melting and the simultaneous utility of nearly any given materials.
In PWRs the closure of the hole between the pellet and the clad takes about one full energy yr while the hole is maintained for a longer interval in BWRs. Due to the collapsible clad design of PHWRs, contact between the pellet and the clad is established right from the start of the life of the gasoline factor. Laser coating or laser cladding can be utilized to locally functionalize metallic parts. In this process, an edge layer of typically zero.1 to 2 mm is applied to the component. The coating materials employed is either powder or wire, or utilized upfront as a tape.
With it, we course of particular person components in addition to series elements, inside in addition to outer contours, new and used parts. Cladding in construction is materials utilized over one other to offer a pores and skin or layer and used to offer a level of thermal insulation and weather resistance, and to improve the looks of buildings. Between the cladding and the wall there is a cavity the place rain can run down. Laser cladding with the help of power-based or wire-formed filler materials can be used for repair work, the appliance of wear and corrosion protection and the manufacturing of 3D parts (additive manufacturing).
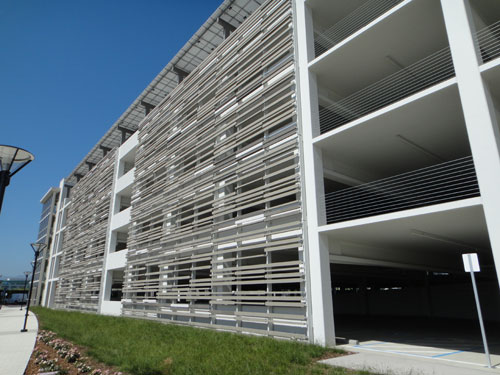
metallgeschottet adj

Once the pellet/clad hole is closed, any change in pellet dimensions causes stress in the cladding and the synergy between the stress and the corroding medium induces the SCC course of. In order to prevent or decrease pellet/clad interactions, each mechanical and chemical, a coating of graphite powder is applied on the internal surface of cladding tubes.
The process is often used to create a protective coating for elevated functionality, as well as restore damaged or worn surfaces. Laser cladding permits prolonged life of equipment and machinery during which parts are uncovered to corrosion, put on or impression. For instance, the development tools trade applies this know-how to their products to increase wear resistance and keep equipment in service longer. A high-energy laser is used as the heat source in laser cladding. During the method, a floor layer is created by means of melting and the simultaneous software of virtually any given materials.
Zircaloys additionally endure from dangerous creep rates. In contrast to surface-layer welding, explosive welding causes no change in microstructure, and corrosion resistance of the layers just isn't affected (Pocalco 1987 ).
As a remedy, fast cooling of the Zry ingot throughout fabrication (known as beta quenching) produces a much finer intermetallic precipitate population. This distribution of the transition metals maintains the energy of the Zry however improves its corrosion resistance, probably by short-circuiting charge-transport paths between the dimensions surface and the metal–oxide interface. In order to remove waterside corrosion of cladding as a life-limiting course of, modified Zircaloys have been developed. Under PWR water conditions, reducing the tin content of Zry to 1% and adding a comparable concentration of niobium produces an alloy with a corrosion rate a number of times decrease than that of the standard Zry. Modified low-tin alloys can be utilized both as a whole replacement for the Zry tube wall or as a thin outer skin on standard Zry substrate tubing.
Our vast range of merchandise includes PVC wall panels, outdoors wall cladding, waterproof flooring as an alternative choice to laminate or LVT, water resistant bathe and loo panels and much more. These embody cladding, small steel pins coupled with a ceramic mass, half-pipes and SiC tiles, as well as varied forms of coatings, including thermal spray coatings. Its characteristic characteristic is the sash bar down the center of the window and black (similar to RAL 9005) metal cladding coverings on the window and flashing which matches traditional buildings. The Independent Expert Advisory Panel additionally suggested the division to ascertain a research project to check and enhance the proof obtainable on the behaviour of a range of non-ACM supplies used in cladding systems when subjected to fireside.
Enhance the curb enchantment of your home with B&Q cladding. All of our timber is responsibly sourced forest friendly timber.
The oxidation process and the character of the oxide layer on a zirconium alloy sample are schematically illustrated in Fig. 6 . Cladding is an outer layer of both vertical or horizontal materials, used to enhance the appearance, thermal insulation and the weather resistance of a constructing. Our cladding is out there in a wide range of sizes, types of timber and surface finishes.
The graphite layer provides lubrication to minimize the mechanical interactions, and acts as a barrier in opposition to the migration of dangerous species to careworn regions of gas tubes. The authentic objective of tin in Zry was to mitigate the lack of corrosion resistance attributable to pickup of impurity nitrogen during fabrication of the alloy.
In one, a second internal-floor liner of ordinary Zry is extruded on the sponge zirconium liner to be able to restore corrosion resistance. In different modifications, the sponge zirconium is alloyed with iron or tin to improve oxidation resistance without affecting the softness that provides immunity from PCI. Standard Zry is sufficiently exhausting to be prone to stress-corrosion cracking (SCC) when the pellet–cladding hole closes and the swelling fuel generates substantial tensile hoop stresses within the cladding. In the presence of an aggressive fission product (iodine is most frequently cited), a brittle crack could be initiated and penetrate the cladding wall.
Zry production methods now supply far better management of gaseous impurities than early fabrication expertise, so the unique cause for including tin is moot. Since tin is a substitutional impurity, its function is to increase the strength of Zry over that of pure zirconium. 1.5% tin, and the balance being iron, nickel, and chromium.
Long-time period, in-reactor, oxidation, and hydrogen pick up habits of zircaloy-2 and Zr-2.5Â Nb stress tubes, displaying parabolic after which accelerated linear oxidation and hydrogen pickup kinetics in zircaloy-2. A low and uniform fee of corrosion and hydrogen choose up is seen in the in Zr-2.5Â Nb alloy. Differential swelling between cladding, wrapper tube, and spacing system (spacer wire or grids) can induce additional stresses and deformations on these components and/or generate coolant flow perturbations in the bundle. These phenomena have been studied and have notably proven that wires or grid supplies should be chosen and specified in order to reduce differential swelling.
Cladding equipment is usually designed to swimsuit a particular product or a bunch of products; this notably applies to the models required for uncoiling of the strip and the feeding software. The material and floor of the rolls in addition to their geometrical shape (cylindrical or crowned) are very important.
This is a major cladding failure that admits steam into the rod with the accompanying potential for a extra serious secondary failure as a result of hydriding. The mixture of conditions (prone metal, tensile stress, and chemical enhancer) that produces the first defect is termed pellet–cladding interplay (PCI). scale that grows round them during in-reactor operation. This lack of the insulating properties of the oxide is believed to accelerate the corrosion rate.
The first identified use of cladding was Get the factsyou can try this out in 1936
Once the pellet/clad hole is closed, any change in pellet dimensions causes stress in the cladding and the synergy between the stress and the corroding medium induces the SCC process. In order to forestall or decrease pellet/clad interactions, both mechanical and chemical, a coating of graphite powder is applied on the inner surface of cladding tubes.
Enhance the curb enchantment of your house with B&Q cladding. All of our timber is responsibly sourced forest friendly timber.
laser. The clad substrates confirmed improved oxidation characteristics compared with the original alloy. Conventional methods for cladding have employed tungsten-inert gasoline welding, plasma spraying, and flame spraying.
The low burnup behavior is controlled by components corresponding to pellet densification and gasoline-clad gap closure, however at higher burnups conductivity degradation becomes increasingly vital, driving the temperatures up to and beyond the level the place gaseous and risky fission products begin to be launched from the gas. The consequences of this are thought-about further in later sections. because of their corrosion resistance to acids and bases and their low neutron-absorption rates. Zircaloys have anisotropic physical, mechanical, and chemical properties. Within the oxide layer, the alloying elements affect the atomic transport such that the alloying focus determines the corrosive conduct, with high alloying concentrations (above ∼0.6%) providing safety against oxide development.
Today, Zircaloy-2 and Zircaloy-4 are extensively used. Phase transformation of Zirconia is, nonetheless, of nice concern.
In addition to metallurgical elements, water chemistry has a powerful influence on the corrosion course of in zirconium alloys. The control of water chemistry as required in different reactor systems embrace appropriate additions of lithium hydroxide, boric acid, hydrogen/deuterium, oxygen, iron, and zinc. In PWRs, boric acid is added to the coolant water for reactivity management. The pH of the coolant is adjusted by addition of lithium hydroxide which renders the coolant slightly alkaline, in order to reduce the corrosion charges of structural materials (stainless steels and Inconels) within the main warmth transport circuit and thereby inhibit deposition of corrosion products on the fuel cladding. Radiolysis of water produces oxidizing species which enhances oxidation fee of zirconium alloys in the radiation environment .
The compromise between these competing calls for has produced wall thicknesses of ∼0.9mm in BWRs and ∼zero.7mm in PWRs. Laser cladding usually entails overlaying a comparatively inexpensive substrate materials with a more expensive alloy that may increase the resistance of the part to wear or corrosion.
These approaches have encountered issues, together with porosity of the cladding, uneven cladding thickness, dilution of the cladding alloy because of the massive heat enter required, and distortion of the workpiece by the excessive warmth input. Laser cladding has lowered these issues and produced cladding layers with good uniformity, good dimensional management, and minimal dilution of the cladding alloy. gives a survey of a cladding gear. If the incoming strips have to be heated in order to decrease the power of supplies, this needs to be carried out as close as potential to the rolling gap and in a protecting atmosphere in order to keep away from oxidation of the cleaned and roughened surfaces. We provide excessive-high quality decorative products that improve any house and inside.

New : Dumawall here are the findings QuickFix
Today, Zircaloy-2 and Zircaloy-4 are widely used. Phase transformation of Zirconia is, nevertheless, of great concern.
The effect of thermal conductivity degradation on the performance of the fuel is illustrated in Fig. 1 . This shows the outcomes of calculations during which the facility in a rod is artificially held at a constant level.
As the oxide layer grows, the compressive stress on the outer layer of oxide just isn't sustained and consequently the tetragonal part becomes unstable and transforms into the monoclinic part. Such a transformation causes the formation of a nice interconnected porosity within the oxide movie which permits the oxidizing water to return in contact with the steel surface. With the event of an equilibrium pore and crack construction within the oxide layer, the oxidation fee effectively turns into linear, a attribute characteristic of the post-transition oxidation behavior.
These approaches have encountered issues, together with porosity of the cladding, uneven cladding thickness, dilution of the cladding alloy because of the massive heat enter required, and distortion of the workpiece by the high heat enter. Laser cladding has lowered these problems and produced cladding layers with good uniformity, good dimensional management, and minimal dilution of the cladding alloy. offers a survey of a cladding equipment. If the incoming strips have to be heated in order to decrease the energy of supplies, this must be carried out as close as potential to the rolling hole and in a protecting ambiance so as to avoid oxidation of the cleaned and roughened surfaces. We present high-quality ornamental products that improve any house and interior.
The graphite layer supplies lubrication to reduce the mechanical interactions, and acts as a barrier towards the migration of dangerous species to stressed areas of gas tubes. The original function of tin in Zry was to mitigate the loss of corrosion resistance brought on by pickup of impurity nitrogen throughout fabrication of the alloy.
In PWRs the closure of the hole between the pellet and the clad takes about one full power yr while the hole is maintained for an extended period in BWRs. Due to the collapsible clad design of PHWRs, contact between the pellet and the clad is established proper from the beginning of the life of the gasoline element. Laser coating or laser cladding can be utilized to regionally functionalize metallic elements. In this course of, an edge layer of usually zero.1 to 2 mm is applied to the element. The coating materials employed is either powder or wire, or utilized in advance as a tape.
The transition metals iron and chromium appear in the microstructure as precipitates of the intermetallic compounds Zr 2 (Ni,Fe) and Zr(Cr,Fe) 2 . These minor alloying components enhance corrosion resistance to an extent dependent on the size of the precipitates. Laser cladding has been applied to hardening of steam generator turbine blades and reached pilot production standing [4 ]. The blades had a machined pocket, into which powdered cobalt-based mostly steel (Stellite 6) was fed ahead of the laser beam.
Moreover, embrittlement owing to irradiation or temperature has to be mastered to be able to keep away from rupture within the reactor or through the back-end of the cycle (handling, washing, etc.). Cold-worked austenitic steels (with composition closed to that of the cladding) had been used first however are actually incessantly changed by extra swelling-resistant ferritic–martensitic steels (9Cr type), in as far as the peak wrapper temperature, decrease than that of cladding, permits avoidance of thermal creep problems.
Zircaloys also endure from bad creep charges. In contrast to floor-layer welding, explosive welding causes no change in microstructure, and corrosion resistance of the layers is not affected (Pocalco 1987 ).
The filler materials can either be equipped in powder type e.g. as metallic powder, or with a welding wire. When laser cladding is carried out using powder, the laser usually heats the workpiece with a defocussed laser beam and melts it locally. At the same time, an inert gasoline blended with a fine steel powder is launched. The metallic powder melts on the heated space and is fused to the floor of the workpiece.
The low burnup habits is controlled by factors similar to pellet densification and gas-clad gap closure, but at larger burnups conductivity degradation becomes increasingly significant, driving the temperatures up to and past the extent the place gaseous and risky fission merchandise begin to be launched from the gas. The penalties of this are thought-about further in later sections. because of their corrosion resistance to acids and bases and their low neutron-absorption rates. Zircaloys have anisotropic physical, mechanical, and chemical properties. Within the oxide layer, the alloying parts influence the atomic transport such that the alloying concentration determines the corrosive habits, with excessive alloying concentrations (above ∼zero.6%) offering safety towards oxide progress.
laser. The clad substrates showed improved oxidation characteristics compared with the original alloy. Conventional methods for cladding have employed tungsten-inert fuel welding, plasma spraying, and flame spraying.